Tipos de roscas
Técnicamente una rosca es una arista
de sección uniforme que tiene la forma de un helicoide sobre la superficie
externa o interna de un cilindro, o con la forma de una espiral cónica sobre la
superficie externa o interna de un cono, o de un cono truncado. Al roscado de
un cilindro se lo llama rosca cilíndrica y al efectuado en un cono o en un cono
truncado, rosca cónica
-Tipo de paso grueso: UNC y NC. Se recomienda para usos generales donde no se requieren pasos más finos.
-Tipos
de paso fino: UNF y NF. Esencialmente igual a la primitiva serie SAE,
recomendada para la mayoría de los trabajos en la industria automotriz y
aeronáutica.
-Tipos
de paso extrafino: UNEF y NEF. Igual que la vieja serie SAE fina, se recomienda
par usar en materiales de paredes finas o cuando se requiere un gran número de
filetes en una longitud dada.
-Tipo
de ocho hilos. SN. En esta serie hay ocho hilos por pulgada todos los diámetros
desde 1 a 6 pulgadas . Esta serie
es recomendada para las uniones de cañerías, pernos de pistón y otros cierres
donde se establece una tensión inicial en el elemento de cierre para resistir
presión de vapor, agua, etc.
-Serie
de doce filetes; 12UN y 12N.
Esta serie tiene doce hilos por pulgada para diámetros que van de ½ a 6 pulgadas . Los tamaños
de ½ a 1 ¾ pulgadas se usan en calderería.
-Serie
de dieciséis filetes: 16UN y 16N. Esta serie tienen dieciséis por pulgada y
abarca diámetros que van desde ¾ hasta 6 pulgadas . Se usan en
una amplia variedad de aplicaciones, tales como collares de ajuste, retén, etc.
que requieren un filete muy fino.
-Rosca
amé.
-Rosca
de diente de sierra.
-Rosca
cuadrada.
-Rosca
Brown Sharpe.
Estos últimos cuatro
tipos de rosca, se usan principalmente para transmisión de potencia y
movimiento.
-Rosca
normal americana para tubos: es la rosca cónica normal que se usa en uniones de
caños en Estados Unidos.
-Rosca
Métrica Normal Internacional: esta rosca se usa mucho en tornillos de medida
métrica fabricados en el continente europeo.
Las características principales de las roscas son:
-
Tipo de rosca: Pueden
ser triangulares cuadradas, trapezoidal, redonda, diente de sierra etc.…
-
El paso: es la
distancia que hay entre dos filetes consecutivos.
-
Diámetro
exterior de la rosca: Es el diámetro exterior de tornillo.
-
Diámetro
interior
-
Diámetro de
flanco
-
Angulo de hélice
de la rosca
En la rosca métrica la sección del filete es un triangulo equilátero cuyo Angulo
vale 60º.
El fondo de la rosca es redondeado y la
cresta levemente truncada.
El lado del triangulo es igual al paso.
Su diámetro exterior y el paso se miden en
milímetros, siendo el paso la longitud que avanza el tornillo en una vuelta
completa.
Se expresa de la siguiente forma:
M24x3
la M significa rosca métrica, 24 es el valor del diámetro exterior en Mm
y 3 es el paso en Mm.
Acotación de las roscas.
Aquí dejo este link con un documento extenso de normalización
y acotación de prácticamente todas las roscas. “punto 1 elementos roscados”
Tablas de mecanización
de roscas
Por ejemplo en las roscas de la práctica
son M8 y M10.
Las brocas que se han afilado para utilizarlas son de diámetros 7mm y
La varilla a mecanizar tiene que tener de diámetro
Practica a realizar.
Se
mecanizará una pieza de 60x60x10 Mm mediante corte manual
(Sierra
de mano)
A
continuación se le realizarán 2 taladros situados en la diagonal de manera
simétrica y con una separación entre ambos de 30mm. Se procede a realizar el
roscado de los taladros, uno de ellos con M8 y el otro con M10
2ºse
marca la diagonal en ella y con un granate se marca los puntos a perforar.
3º Se taladra la pieza,
4º Mediante un macho para roscar a mano m8 y m10 y echandole un poco de aceite para que se deslice mas facil y se desgaste menos se hace la rosca interior. Utilizando gradualmente los tre machos.

5º Ahora se cortan las varillas para hacer los tornillos de 8 y 10 mm de diametro.
6º Con una terraja m8 y m10 respectivamente y un paso de 1,5 se roscan los tornillos echando aceite también.
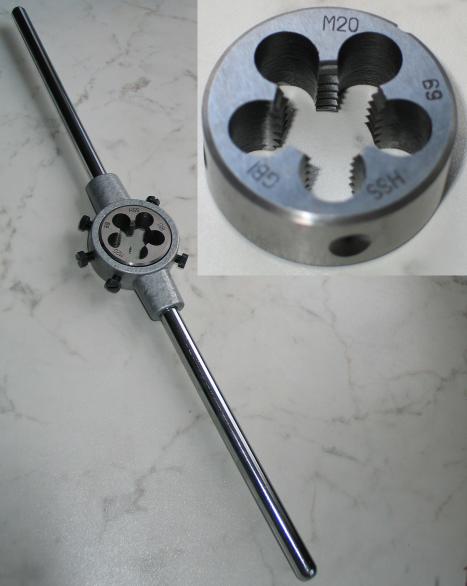
Posteriormente se liman los extremos de los tornillos hasta dejarlos cuadrados.
Afilado de brocas.
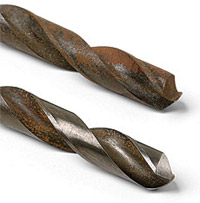
Datos a tener en cuenta para afilar las brocas:
El ángulo de la punta a de ser de 118 grados
Cada cara de la punta de la broca debe inclinarse hacia abajo unos 12 grados
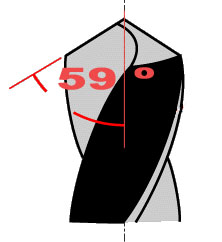
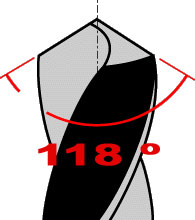
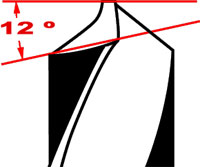
Al usar la piedra de esmeril en el afilado debe usarse la protección adecuada para este trabajo como puede ser el uso de guantes y gafas protectoras.
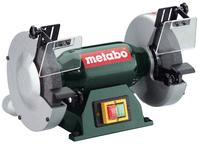